Clearing Up Misconceptions About Perforated Tape
Composite materials — carbon fiber, fiberglass, kevlar, PEEK, and others — are used in numerous industries worldwide for countless products ranging from sporting goods and auto parts to household goods and even energy-related applications. And thanks to their strength, temperature resistance, chemical resistance, and other advanced features over traditional materials like steel, their use will only continue to grow.
A common application for composite materials is the production of various types of tubing. To ensure these materials deliver the high levels of performance their customers expect, companies using composites in their production — whether it’s a wet layup process or using prepregs — must rely on resin between the material layers to create the necessary bond and compress them. This is to de-bulk the end product, eliminate voids and air pockets, and ensure the material is defect-free.
One of the most common solutions today for successful compaction is hi-shrink tape, which constricts the underlying structure as heat is applied during the curing process. The tape is wrapped around the material — with sufficient overlap to ensure proper compaction — and placed in an oven, where it begins to shrink.
As a result, the pressure applied by the tape forces resin through the composite matrix and between the layers of the material, bringing them as close together as possible and filling any voids. And while the resin plays a key role in achieving a tight bond, oftentimes it is important to de-bulk as much as possible.
Hi-Shrink tapes come in various versions, release coated, non-coated, and perforated. Perforated release films are commonly used in the composite industry to help remove resin away from the composite surface and onto bleeder cloth where the resin is soaked up. Perforated shrink tapes are often sought out for the same reasons a processor wants to use perforated release films. This is where the most common misconception about perforated tape arises: often, the perception is that perforated tape will allow the excess resin to escape through the perforations. While there may be some squeeze-out through the perforations, this is unlikely and isn’t the intended use of the tape. (Despite the perforations, the true bleed-out will occur between the tape layers, where it can then be removed with the tape after curing — if the tape is to be removed at all.)
The true benefit of perforated tape is due to what’s happening in the material: certain composite layups and wet-winds will produce volatiles — gasses and vapors — that must be allowed to escape, otherwise, they’ll create imperfections like bubbles, dry spots, or de-lam (when parts of the matrix aren’t bonding) that can impact material performance. This is where perforated tape excels. Allowing the volatiles to escape the layup contributes to more uniformity in the lamination and overall consolidation of the composite material layers. And the more outgassing involved, the more beneficial perforated tape will be.
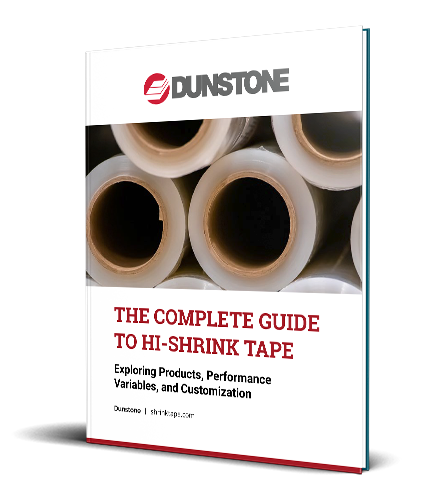
Download our Complete Guide to Hi-Shrink Tape
Our guide to Hi-Shrink Tape is packed with product details, application recommendations, and more.
An Example of Improvement Through Perforated Tape
A Dunstone customer in the manufacturing space was using composite material to produce utility poles — a solution where climates, insects, location, and other factors make using wood poles unfavorable. The company was using a wet layup process in which individual fibers were being wrapped around a core that is removed after curing.
During the early stages of production, a significant amount of resin was added to the fibers to achieve full saturation. This was then wrapped with more material followed by more resin. Once the product reached the desired outside diameter for fiber content, the company wrapped it in non-perforated hi-shrink tape ahead of oven curing.
While this standard shrink tape was working well and led to proper consolidation of material, they were still getting voids in the layup fibers and dry spots on the surface. This was due to their particular resin producing substantial gaseous volatiles that were getting trapped under the tape. Apart from the appearance and structural issues this posed, it was also problematic because the pole surfaces weren’t painted or otherwise covered up — the post-cure product was what their customers received.
They contacted Dunstone looking for a solution to improve surface consistency and structural integrity while eliminating these voids in the matrix. We recommended our perforated tape, and immediately upon the company’s next run of poles, there were no voids in the matrix or surface dry spots.
More: Explore another example of how hi-shrink tape supported an infrastructure company.
Put Our Perforated Tape to Use in Your Next Application
For more than 60 years, Dunstone has been producing multiple lines of innovative shrink tapes and films for multiple industries. Our 200 Series, in particular, is ideal for perforation tape needs, and our 200 line is available in widths from 0.5” to 2.5” as standard (custom widths up to 20”) with a 0.02” thickness that minimizes the height of leftover lines (aka “cello lines”) on cured parts, keeping surface appearance consistent. It is suitable for cure temperatures up to 165ºC (330ºF). For perforated tape needs, our 220R and 220S specific products are ideal.
More importantly, however, we can customize the shrink percentage on this tape to suit your needs. Percentages range from 5% to 20% and are tailored to your unique application based on the amount of compaction force required. The 200 Series is also available in uncoated, 1-side release coated, or 2-side release coated variants.
Learn more about our 200 Series line of hi-shrink tapes.
Request a sample of perforated tape from our 200 line today.